Vol.5 MATERIAL FOR TOOLING
Selection of tool material (Type of material) is very important in terms of the quality of the processed product and the tool life (processing cost).
This time, we summarized the typical material for tooling.
MATERIAL OF PUNCH
We use the following material for punch body.
- ・D2(SKD)
- ・M2(SKH)
Fig.1 Material properties of the punch
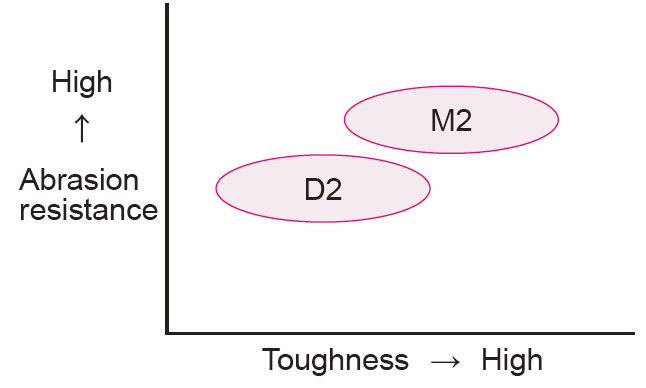
Characteristics of each steel
D2 (SKD)
It is a typical tool steel for sheet metal processing which is excellent in mechanical properties and heat treatment characteristics.
We adopt Super-subzero treatment to further improve wear resistance.
M2 (SKH)
It is one of the most widely used materials among M2.
Compared to D2, it is a material excellent in abrasion resistance, impact resistance and toughness.
It is suitable materials such as stainless steel and a large amount production.
MATERIAL OF DIE
We use the following material for die.
- ・Improved D2
- ・M2(SKH)
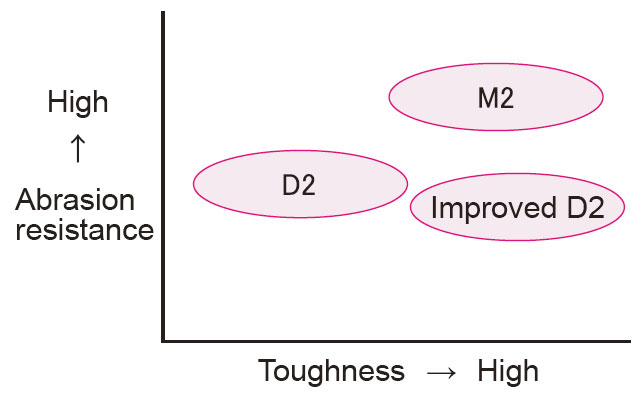
Characteristics of steel
Improved D2
A material with improved toughness and chipping resistance by refining carbides. It has toughness equal to or higher than that of M2.
HOW TO SELECT MATERIAL
Selection of the material of the tool is done by processing conditions (such as the material of sheet metal, the number of hits and the accuracy of product).
The guides of selection are as follows.
GUIDE FOR SELECTING D2 | GUIDE FOR SELECTING M2 |
|
|
In case of large number of production or difficult-working materials, it is recommended to use in combination with super-dry punch or coating process tools.
Not only the insufficient strength of the tool but also other factors
(such as sludge rise, misalignment of the turret,insufficient mounting of the tool,etc.)
can be considered as the cause of the breakage of the tool.
We recommend that you select the material after carefully investigating the cause of the damage.
(See our TECHNICAL GUIDE “2-2) Life countermeasure for tooling” for more detail about SDP.)
OTHER MATERIAL FOR TOOLING
CARBON STEELS FOR MACHINE STRUCTURAL MATERIAL
It is one of the representative steel types of metal materials.
In the tool, it is used for part that is not processed directly on the material.
(Tool head, retainer collar etc.)
CHROMIUM MOLYBDENUM STEEL(SCM)
It is used for parts that require middle strength. (Guide, ejector of forming tool etc.)
CARBON TOOL STEEL(SK)
It is used for parts that require relatively high hardness. (Key-pin, ejector of forming tool etc.)
ALLOY TOOL STEEL(SKS)
Used for a part this needs equal hardness as D2 steel. (Pin holder etc.)
PDF Download
vol.1 COUNTERMEASURES FOR SLUG PULLING IN PUNCHING PROCESS
vol.2 LIFE COUNTERMEASURE FOR TOOLING
Vol.3 TOOL MAINTENANCE
Vol.4 FORMING TOOL
Vol.5 MATERIAL FOR TOOLING
Vol.6 FOR CLEARANCE OF THE CUTTING DIE
Vol.7 ABOUT TURRET PUNCH PRESS MACHINE
Vol.8 VARIOUS KINDS OF SPECIAL SHAPE
Vol.9 PARTS NAME OF STANDARD TOOLING
Vol.10 EACH NAMES OF FORMING TOOL
Vol.11 MATERIAL PROPERTIES (STEEL)
Vol.12 MATERIAL PROPERTIES
Vol.13 CALCULATION FORMULAS FREQUENTLY USED IN SHEET METAL
Vol.14 HEIGHT ADJUSTMENT FREE TOOL
Vol.15 HOW TO DRAW AND READ DRAWINGS
Vol.16 HOW TO DRAW AND READ DRAWING (PRACTICAL USE)
Vol.17 SHAPE INSTRUCTION FOR FORMING TOOLS(1)
Vol.18 SHAPE INSTRUCTION FOR FORMING TOOLS(2)
Vol.19 CODE MANAGEMENT
Vol.20 BENDING TECHNICAL INFORMATION
Vol.21 TECHNICAL COUNSELING FAQ(1) "COUNTERMEASURES FOR GALLING"
Vol.22 TECHNICAL COUNSELING FAQ(2) "BURRING FOR THREAD FORM"
Vol.23 TECHNICAL COUNSELING FAQ(3) "PITCH OF SINGLE PIERCING"
Vol.24 TECHNICAL COUNSELING FAQ(4) "SHEAR OPTIONS"
Vol.25 TECHNICAL COUNSELING FAQ(5) "HOLDING MARK"
Vol.26 TECHNICAL COUNSELING FAQ(6) "SOLUTION FOR SLUG PULLING OF A SHEET METAL WITH PROTECTIVE FILM"
Vol.27 TECHNICAL COUNSELING FAQ(7) "MATERIAL WARPING PREVENTION DURING"
Vol.28 TECHNICAL COUNSELING FAQ(8) "WARPING PREVENTION OF BLANKING OUT"
Vol.29 TECHNICAL COUNSELING FAQ(9) "COUNTERSINK FOR COUNTERSUNK SCREW"
Vol.30 THE ORDERING GUIDE(1) "HOW TO INSTRUCT SHAPE AND DIMENSIONS"
Vol.31 THE ORDERING GUIDE(2) "REFERENCE KEY DIRECTION"
Vol.32 THE ORDERING GUIDE(3) "ANGLE INDICATION OF ANGLED TOOL"
Vol.33 THE ORDERING GUIDE(4) "SELECT SPECIFICATION OF PUNCH"
Vol.34 THE ORDERING GUIDE(5) "DIE SPECIFICATION SELECTION"