Vol.34 THE ORDERING GUIDE(5) "DIE SPECIFICATION SELECTION"
DIE SPECIFICATION SELECTION
When ordering a die, please select and refer to the following specifications.
SELECTION OF DIE MATERIAL
We have two types of die materials available.
- 1. D2 (Improved D2 steel is standard)
- 2. HSS (High speed steel)
Improved D2 material is a material that has improved toughness and chipping resistance by making micronized carbides.
Unless otherwise specified, the material is D2 steel (improved D2 steel).
However, if wear resistance is required, please specify the die for the high speed steel and the high speed steel for the punch body.
SELECTION OF DIE CUTTING EDGE
Standard die cutting edge specifications are as follows.
(Some models and sizes may differ from the following specifications.)
Name of cutting edge | Shape of cutting edge | specifications | Applications |
Straight edge with straight relief |
![]() |
The cutting edge and relief part are straight. This is a general cutting edge shape. |
Adopted in a round shape. |
Slug catcher (SC) |
![]() |
Cutting edge shape with excellent slug-pulling preventive effect with a reverse-tapered cutting edge. | Adopted for standard square shape and special shape. |
All taper |
![]() |
The shape of the entire cutting edge is tapered. | Adopted in a cyclone die. |
Straight edge with taper relief |
![]() |
The shape of the cutting edge that cutting edge part is straight and relief part is tapered. |
Adopted for blank type, die size with clearance less than 2 mm widths, punch with heel, and s tandard square shape with clearance less than 0.1mm. |
All taper II |
![]() |
Cutting edge shape with two-stage taper shape. | Large-station die suitable for machines with a scrap suction device. |
We have also a die for preventing slug pulling other than the above.
Please contact our tool sales desk for more detail.
SELECTION OF DIE CUTTING EDGE
Refer to Technical Information Vol.30 “Ordering Guide 1” for selection of die clearance.
MEASURES TO PREVENT SLAG PULLING
SLUG CATCHER DIE
By attaching a negative taper (reverse taper) to the die cutting edge and pushing the slug into the die,
we adopt the standard square die as standard.
(Excluding some models and sizes)
- 1. Material is cut off at {A} part.
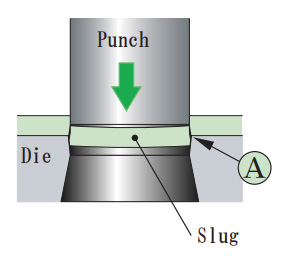
- 2. The slug is compressed in the process of punching at {B} part.
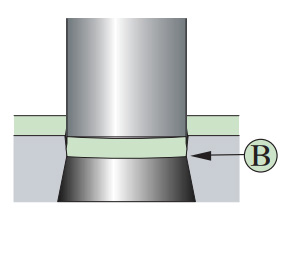
- 3. Drags the slug through the relief.
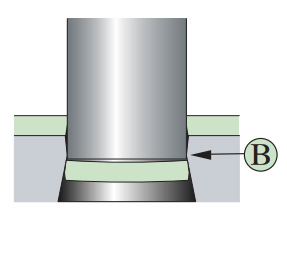
- 4. {B} part is narrower than {C} part so the slug cannot comes up.
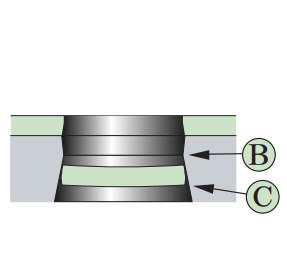
DEPOSITRON TREATMENT
As a prevent slug pulling, this is a process in which cemented carbide alloy was applied to the die cutting edge with a discharge coating.
Slug pulling is prevented by pushing out the slug into the part protruding from the cutting edge.
We use it as a standard for round dies with cutting edge diameters of φ2 to φ4.5.
It is not recommended if the clearance is less than 0.1mm and the workpiece is aluminum.

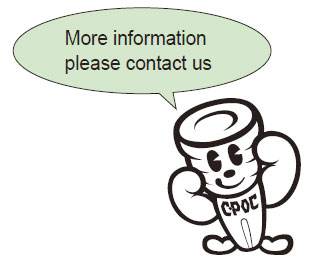
vol.1 COUNTERMEASURES FOR SLUG PULLING IN PUNCHING PROCESS
vol.2 LIFE COUNTERMEASURE FOR TOOLING
Vol.3 TOOL MAINTENANCE
Vol.4 FORMING TOOL
Vol.5 MATERIAL FOR TOOLING
Vol.6 FOR CLEARANCE OF THE CUTTING DIE
Vol.7 ABOUT TURRET PUNCH PRESS MACHINE
Vol.8 VARIOUS KINDS OF SPECIAL SHAPE
Vol.9 PARTS NAME OF STANDARD TOOLING
Vol.10 EACH NAMES OF FORMING TOOL
Vol.11 MATERIAL PROPERTIES (STEEL)
Vol.12 MATERIAL PROPERTIES
Vol.13 CALCULATION FORMULAS FREQUENTLY USED IN SHEET METAL
Vol.14 HEIGHT ADJUSTMENT FREE TOOL
Vol.15 HOW TO DRAW AND READ DRAWINGS
Vol.16 HOW TO DRAW AND READ DRAWING (PRACTICAL USE)
Vol.17 SHAPE INSTRUCTION FOR FORMING TOOLS(1)
Vol.18 SHAPE INSTRUCTION FOR FORMING TOOLS(2)
Vol.19 CODE MANAGEMENT
Vol.20 BENDING TECHNICAL INFORMATION
Vol.21 TECHNICAL COUNSELING FAQ(1) "COUNTERMEASURES FOR GALLING"
Vol.22 TECHNICAL COUNSELING FAQ(2) "BURRING FOR THREAD FORM"
Vol.23 TECHNICAL COUNSELING FAQ(3) "PITCH OF SINGLE PIERCING"
Vol.24 TECHNICAL COUNSELING FAQ(4) "SHEAR OPTIONS"
Vol.25 TECHNICAL COUNSELING FAQ(5) "HOLDING MARK"
Vol.26 TECHNICAL COUNSELING FAQ(6) "SOLUTION FOR SLUG PULLING OF A SHEET METAL WITH PROTECTIVE FILM"
Vol.27 TECHNICAL COUNSELING FAQ(7) "MATERIAL WARPING PREVENTION DURING"
Vol.28 TECHNICAL COUNSELING FAQ(8) "WARPING PREVENTION OF BLANKING OUT"
Vol.29 TECHNICAL COUNSELING FAQ(9) "COUNTERSINK FOR COUNTERSUNK SCREW"
Vol.30 THE ORDERING GUIDE(1) "HOW TO INSTRUCT SHAPE AND DIMENSIONS"
Vol.31 THE ORDERING GUIDE(2) "REFERENCE KEY DIRECTION"
Vol.32 THE ORDERING GUIDE(3) "ANGLE INDICATION OF ANGLED TOOL"
Vol.33 THE ORDERING GUIDE(4) "SELECT SPECIFICATION OF PUNCH"
Vol.34 THE ORDERING GUIDE(5) "DIE SPECIFICATION SELECTION"