Vol.13 CALCULATION FORMULAS FREQUENTLY USED IN SHEET METAL
This time, we summarized a calculation formula that is frequently used in sheet metal,
including the calculation of tonnage.
TONNAGE CALCULATION
In the punch press machine, the allowable tonnage depending on the machine.
Use the calculation formula below to prevent from over tonnage.

Circumference
Round | Shaped |
Diameter x 3.14 | (Length dimension + Width dimension) x 2 |
![]() |
![]() |
Circumference = D x 3.14 | Circumference = (A + B) x 2 |
Shear resistance by material
Material | Shear resistance (kg/mm²) |
Mild Steel | 400 |
SS400 | 450 |
Stainless Steel | 600 |
Aluminum | 200 |
Copper | 300 |
Brass | 400 |
Calculation example
The tonnage when piercing Φ40 to Mild Steel T=1.6mm.

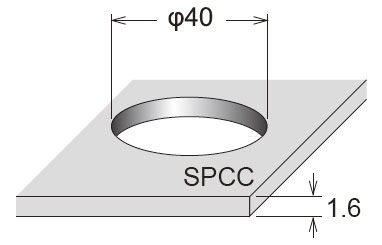
If you do not know the shear resistance, please use about 80% of the shear resistance = tensile strength as a standard.
ADVICE ON ONE POINT
If the tonnage exceeds the allowable tonnage of the machine,
reduce the tonnage by the following method.
- 1.Put shear angle on punch edge. (Allows you to reduce tonnages around 10 to 50% by shear angle.)
- 2.Piercing several times. (Reducing tonnages by piercing several times)
- 3.When using cluster tooling, the tonnages can be reduced by making a difference in length of punch that makes same effect as shear angle.
MAKE A SELECTION OF TOOL STATION
Calculation of the diameter (diagonal dimension) of the cutting edge circumscribed circle is required to select the tool station.
Calculation of diameter (diagonal dimension) of cutting edge circumscribed circle
Rectanglar shape | Rectanglar shape with radius |
![]() |
![]() |
![]() |
![]() |
Rectanglar shape |
![]() |
![]() |
Rectanglar shape with radius |
![]() |
![]() |
ADVICE ON ONE POINT
Normally, the size of the tool station is determined by calculating the dimension of the cutting edge circumscribing circle using the above formula and then comparing it with the turret layout.
However, when processing thick materials, it is necessary to increase the station size by one size to prevent from miss stripping.
CALCULATING PRE-HOLE DIMENSION FOR FORMING
When forming processing, pre-holes may be processed as pre-processing.
In that case, please calculate pre-holes referring to the following calculation formula.
Calculating pre-hole dimension for forming (Reference value for SPCC)
Chamfering | Burring | Burring for tapping | Emboss | ||
Size | Inner Dia. | Pre-hole | |||
![]() |
![]() |
M2.6 | φ2.1 | φ1.2 |
![]() |
M3 | φ2.6 | φ1.5 | |||
M4 | φ3.4 | φ2.0 | |||
M5 | φ4.3 | φ2.4 | |||
M6 | φ5.1 | φ2.8 | |||
Pre-hole =
![]() |
Pre-hole = D+1.8xT-2xH |
Other dimension, Pre-hole = 0.53 x D + 0.1 |
Other dimension, D-(0.6-0.16xT)xH |
Chamfering | Burring | Emboss |
![]() |
![]() |
![]() |
Burring for tapping | ||
Size | Inner Dia | Pre-hole |
M2.6 | φ2.1 | φ1.2 |
M3 | φ2.6 | φ1.5 |
M4 | φ3.4 | φ2.0 |
M5 | φ4.3 | φ2.4 |
M6 | φ5.1 | φ2.8 |
Chamfering | Burring | Emboss |
Pre-hole =
![]() |
Pre-hole = D+1.8xT-2xH |
Other dimension, D-(0.6-0.16xT)xH |
Burring for tapping | ||
Size | Inner Dia | Pre-hole |
Other dimension, Pre-hole = 0.53 x D + 0.1 |
ADVICE ON ONE POINT
Although forming shape is same, pre-hole dimension would be different depending on material.
It is recommended that you try trial machining with reference to the above equation to obtain proper pre-hole dimension.
vol.1 COUNTERMEASURES FOR SLUG PULLING IN PUNCHING PROCESS
vol.2 LIFE COUNTERMEASURE FOR TOOLING
Vol.3 TOOL MAINTENANCE
Vol.4 FORMING TOOL
Vol.5 MATERIAL FOR TOOLING
Vol.6 FOR CLEARANCE OF THE CUTTING DIE
Vol.7 ABOUT TURRET PUNCH PRESS MACHINE
Vol.8 VARIOUS KINDS OF SPECIAL SHAPE
Vol.9 PARTS NAME OF STANDARD TOOLING
Vol.10 EACH NAMES OF FORMING TOOL
Vol.11 MATERIAL PROPERTIES (STEEL)
Vol.12 MATERIAL PROPERTIES
Vol.13 CALCULATION FORMULAS FREQUENTLY USED IN SHEET METAL
Vol.14 HEIGHT ADJUSTMENT FREE TOOL
Vol.15 HOW TO DRAW AND READ DRAWINGS
Vol.16 HOW TO DRAW AND READ DRAWING (PRACTICAL USE)
Vol.17 SHAPE INSTRUCTION FOR FORMING TOOLS(1)
Vol.18 SHAPE INSTRUCTION FOR FORMING TOOLS(2)
Vol.19 CODE MANAGEMENT
Vol.20 BENDING TECHNICAL INFORMATION
Vol.21 TECHNICAL COUNSELING FAQ(1) "COUNTERMEASURES FOR GALLING"
Vol.22 TECHNICAL COUNSELING FAQ(2) "BURRING FOR THREAD FORM"
Vol.23 TECHNICAL COUNSELING FAQ(3) "PITCH OF SINGLE PIERCING"
Vol.24 TECHNICAL COUNSELING FAQ(4) "SHEAR OPTIONS"
Vol.25 TECHNICAL COUNSELING FAQ(5) "HOLDING MARK"
Vol.26 TECHNICAL COUNSELING FAQ(6) "SOLUTION FOR SLUG PULLING OF A SHEET METAL WITH PROTECTIVE FILM"
Vol.27 TECHNICAL COUNSELING FAQ(7) "MATERIAL WARPING PREVENTION DURING"
Vol.28 TECHNICAL COUNSELING FAQ(8) "WARPING PREVENTION OF BLANKING OUT"
Vol.29 TECHNICAL COUNSELING FAQ(9) "COUNTERSINK FOR COUNTERSUNK SCREW"
Vol.30 THE ORDERING GUIDE(1) "HOW TO INSTRUCT SHAPE AND DIMENSIONS"
Vol.31 THE ORDERING GUIDE(2) "REFERENCE KEY DIRECTION"
Vol.32 THE ORDERING GUIDE(3) "ANGLE INDICATION OF ANGLED TOOL"
Vol.33 THE ORDERING GUIDE(4) "SELECT SPECIFICATION OF PUNCH"
Vol.34 THE ORDERING GUIDE(5) "DIE SPECIFICATION SELECTION"