Vol.28 TECHNICAL COUNSELING FAQ(8)
"WARPING PREVENTION OF BLANKING OUT"
This time, we will introduce the prevention of warping (curvature) during blank punching.
WARPING PREVENTION OF BLANKING OUT
Currently, leveler corrects, but is there any good way?
When the plate is punched out, the scraps are generally curved. (See Fig.1)
This is because the material is subjected to bending and bending at the same time as punching,
which causes plastic deformation of the material. (See Fig.2)
Therefore, if the slug is a product like a blank tool, it may be necessary to make adjustments such as passing through a leveler in a later process.
Fig.1 Curved slug when punching
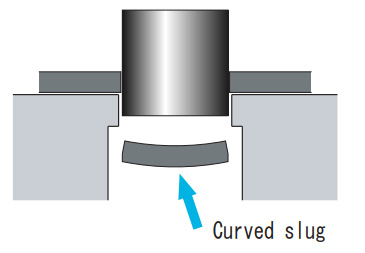
Fig.2 Applied force to the punching time
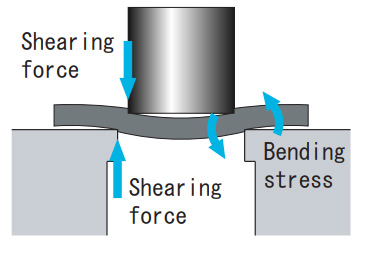
As this measure,
-
1.
Slitting the outline (Periphery).
This method is generally adopted as a method of punching out the outer periphery (contour) of the product rather than punching out the product.
In this case, products are connected by micro joints and separated after processing. (See Fig.3) -
2.
Reduce the die clearance.
As the clearance increases, the bending force applied to the material increases and the curvature increases.
In the case of a blank type, we recommend a clearance slightly smaller than the appropriate clearance.
However, if the clearance is too small in the case of a thick plate, the burden on the tooling will increase and it may also cause damage to the tooling. -
3.
Re-grind early.
Even when punched with a worn cutting edge, the bending force is increased and the curvature is greater.
We recommend re-grinding early and punching with a sharp cutting edge.
Fig.3 Micro joint processing
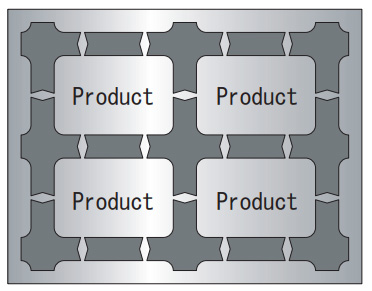
-
4.
Adjust the output length of the urethane kicker.
Even in the case of the blank type, a urethane kicker may be attached to the punch depending on the shape and size of the cutting edge,
in order to prevent the phenomenon that the blank product is lifted without being dropped out
(It is called slug pulling). As a result, depending on the material and thickness of the workpiece,
it is possible that deformation such as warpage may occur in the blank product.(See Fig.4)
Fig.4 Adjust the length of slug ejector
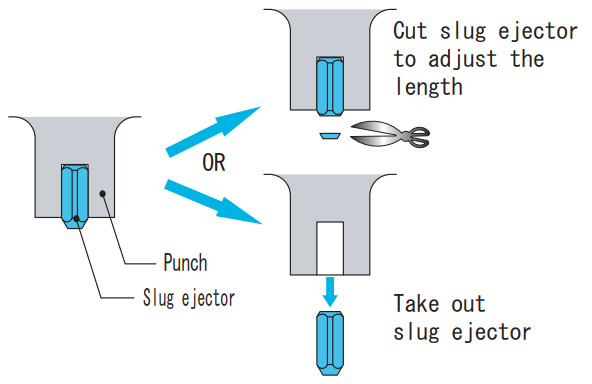
-
5.
Back pressure
his is a method of correcting the curvature of the material by applying reverse pressure to tool and applying back pressure.
(See Fig.5) Half sheared is done in this process, and it is pierced in another process.
Fig.5 Tooling with back pressure
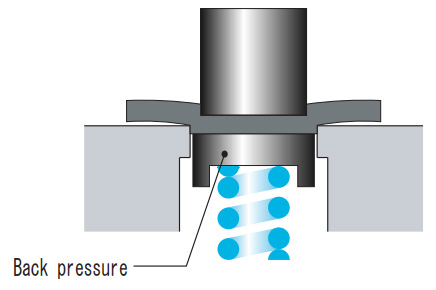
-
6.
To strengthen the holding force.
By using 1 bigger station size and increasing the plate pressing force,
the bending force of the workpiece is suppressed and deformation is reduced.
-
7.
If there is a hole inside the product (in the form of a washer),
a greater curvature will occur.
Also, if there is a hole closer to the product's outer periphery (outline),
there may be distortion in the area between the outer periphery and the hole. (See Fig.6)
Do the drilling in a post process other than punching, or pierce the outline near the hole first.Fig.6 Holes close to the edge of product outline
-
8.
Do not attach shear angles to the blank type.
When punching with a punch with a shear angle,
the blank is deformed by the shear angle.
Always grind the punch surface (the surface that the material hits) flat.
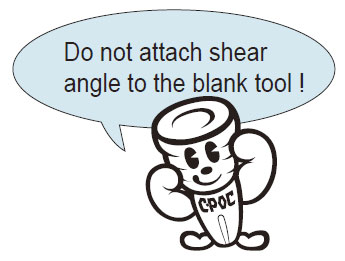
vol.1 COUNTERMEASURES FOR SLUG PULLING IN PUNCHING PROCESS
vol.2 LIFE COUNTERMEASURE FOR TOOLING
Vol.3 TOOL MAINTENANCE
Vol.4 FORMING TOOL
Vol.5 MATERIAL FOR TOOLING
Vol.6 FOR CLEARANCE OF THE CUTTING DIE
Vol.7 ABOUT TURRET PUNCH PRESS MACHINE
Vol.8 VARIOUS KINDS OF SPECIAL SHAPE
Vol.9 PARTS NAME OF STANDARD TOOLING
Vol.10 EACH NAMES OF FORMING TOOL
Vol.11 MATERIAL PROPERTIES (STEEL)
Vol.12 MATERIAL PROPERTIES
Vol.13 CALCULATION FORMULAS FREQUENTLY USED IN SHEET METAL
Vol.14 HEIGHT ADJUSTMENT FREE TOOL
Vol.15 HOW TO DRAW AND READ DRAWINGS
Vol.16 HOW TO DRAW AND READ DRAWING (PRACTICAL USE)
Vol.17 SHAPE INSTRUCTION FOR FORMING TOOLS(1)
Vol.18 SHAPE INSTRUCTION FOR FORMING TOOLS(2)
Vol.19 CODE MANAGEMENT
Vol.20 BENDING TECHNICAL INFORMATION
Vol.21 TECHNICAL COUNSELING FAQ(1) "COUNTERMEASURES FOR GALLING"
Vol.22 TECHNICAL COUNSELING FAQ(2) "BURRING FOR THREAD FORM"
Vol.23 TECHNICAL COUNSELING FAQ(3) "PITCH OF SINGLE PIERCING"
Vol.24 TECHNICAL COUNSELING FAQ(4) "SHEAR OPTIONS"
Vol.25 TECHNICAL COUNSELING FAQ(5) "HOLDING MARK"
Vol.26 TECHNICAL COUNSELING FAQ(6) "SOLUTION FOR SLUG PULLING OF A SHEET METAL WITH PROTECTIVE FILM"
Vol.27 TECHNICAL COUNSELING FAQ(7) "MATERIAL WARPING PREVENTION DURING"
Vol.28 TECHNICAL COUNSELING FAQ(8) "WARPING PREVENTION OF BLANKING OUT"
Vol.29 TECHNICAL COUNSELING FAQ(9) "COUNTERSINK FOR COUNTERSUNK SCREW"
Vol.30 THE ORDERING GUIDE(1) "HOW TO INSTRUCT SHAPE AND DIMENSIONS"
Vol.31 THE ORDERING GUIDE(2) "REFERENCE KEY DIRECTION"
Vol.32 THE ORDERING GUIDE(3) "ANGLE INDICATION OF ANGLED TOOL"
Vol.33 THE ORDERING GUIDE(4) "SELECT SPECIFICATION OF PUNCH"
Vol.34 THE ORDERING GUIDE(5) "DIE SPECIFICATION SELECTION"