ベンディング金型編
1-11)曲げ加工の問題点④(スプリングバック対策)
今回はスプリングバックとワークの反り対策について考えてみましょう。
スプリングバック対策
スプリングバックとは、曲げ加工後に圧力が除かれると、曲げ角度が跳ね返ってくる現象です。
代表的な対策例を3つ挙げてご説明します。
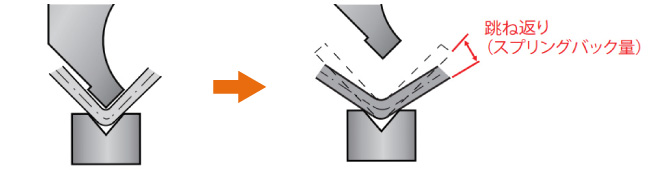
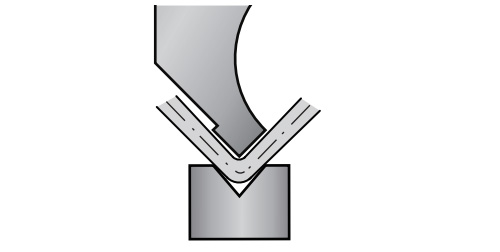

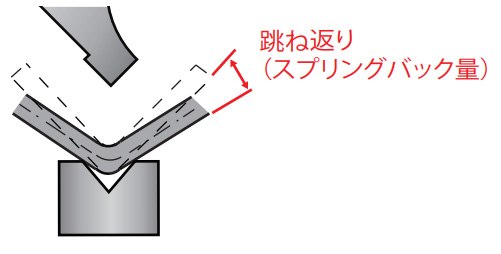
対策① 1回のストロークで2回の曲げを行う2段曲げ
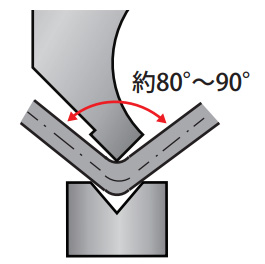
① 1段階目は予備曲げとして、80°~ 90°程度曲げる。
一旦加圧を緩め、故意にスプリングバックを起こす。


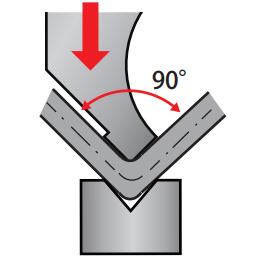
② そのままパンチを上昇させず、
再度加圧を行う事で指定の角度を出します。
対策② コーナー抑え込み方式(ストライキング)
ストライキング方式とも言われ、パンチの刃先面の両隅にストライキングと呼ばれる出っ張りを設け、 コイニング方式の曲げに近づける事で、スプリングバックを防止します。
※この方式はパンチが特殊形状になりますが、多量生産に適しています。
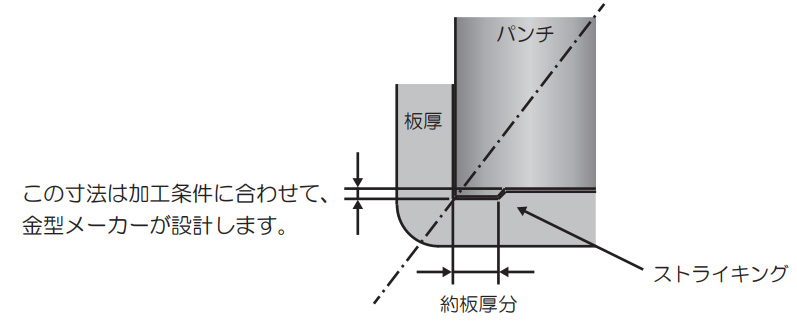
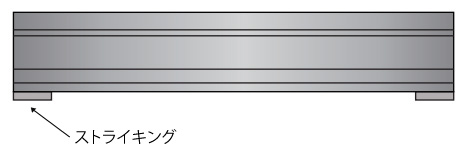
対策③ Vノッチを設ける(開先加工)
加工材にVノッチ(V字型のくぼみ)を前工程であらかじめ付けておき、その部分にパンチの刃先があたる様にプレスする方法。
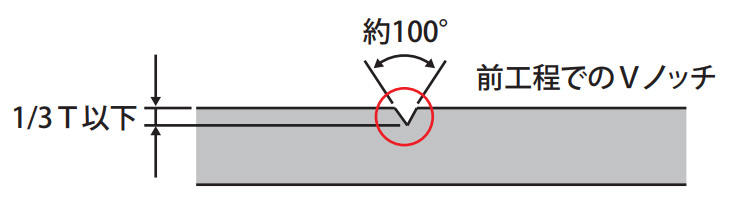

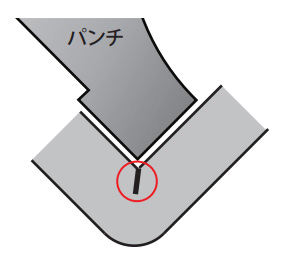
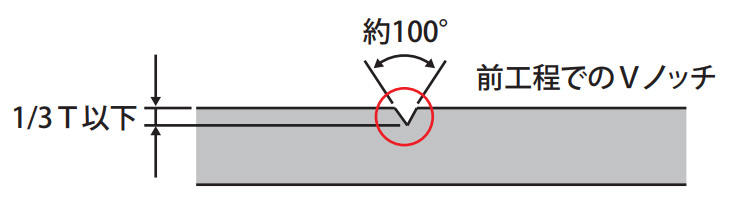

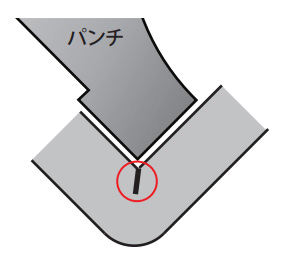
ワークの反り対策
-
①使用する金型は同時に再研磨を行う。
※ 複数の金型を並べて使用する事が多い為、金型同士の通り精度を出して加工を行いましょう。 - ②コイニングで曲げる。
-
③旧式機械をご使用の場合、反りが発生する箇所のダイとホルダーの間にシムを挟み調整する。
一度曲げた後、再度曲げを行う為、金型の位置合わせやシムの厚み設定等の注意が必要です。 - ④旧式機械をご使用の場合は、加圧シリンダーがある位置をさけて曲げ加工を行いましょう。
- ※③と④は現在の機械では機械本体で対策がとられており、コンソール上の調整や、機械本体の機構上で修正可能です。
旧式機械を使用している場合の注意点
- ■長尺であるほど、手作業の修正が必要になる。
- ■目安として、1m以上の曲げに対してSPCCで0.5mm、SUSで1.5~2.0mmの誤差が出る。
- ■しかし、金型や機械の仕様、被加工材により異なる為、自社でのデータ取りが必要である。
板金機械による切断方法と反りの傾向
切断方法 | タレパン・プレス機による切断 | レーザー加工による切断 |
![]() |
![]() |
|
反りの方向 | 両端が上向き | 両端が下向き |
反りの度合い | レーザー加工より小さい | タレパン・プレス機より大きい |
曲げ速度と反り | 曲げ速度を遅くすると反りが小さくなる傾向にある | 曲げ速度を速くすると反りが小さくなる傾向にある |
材質と反りの大きさ | SPCC < SUS | SPCC < SUS |
※板厚・材質により、反りの大きさは異なります。
まとめ
曲げ加工の問題点は、「1-10)曲げ加工の問題点③(クラック・割れ対策)」を含め、
「スプリングバック」、「角度不良」などに起因することが多く、
計算や、金型精度だけでは問題解決できず、「経験」による対処が多く存在するのが実状です。
機械の進歩や解析ソフトも進化していますが、実際はトライ後の補正は欠かせません。
状況に応じた様々な経験ノウハウに基づく対応が必要となります。