vol.15 ABOUT TOOL MANAGEMENT
(EXAMPLE OF TOOL MANAGEMENT, EXTENDING TOOL LIFE)
This time, we will consider “management” of tool.
It is necessary to know the current status of the tools owned and keep them ready for use.
For that purpose, it is important to visualize two points: (1) Tool basic information (tool type and quantity) and (2) Tool state.
EXAMPLE OF TOOL MANAGEMENT
- ◆Ranks and manages the status of tools.
- A: Good product
B: Caution products (Scratches etc.)
C: Regrinding required
D: Unusable item Use a label printer to display and manage the date of regrinding and the presence or absence of rust at a glance. - Press brake tools are considered to be based on multiple units regardless of the degree of use, so the quality of the sheet metal is easily affected directly. Let's manage tool firmly on a daily basis.
Example of tidy tool
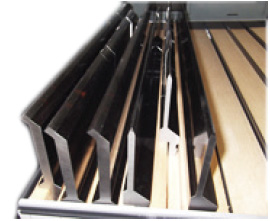
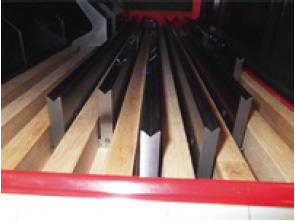
EXTENDING TOOL LIFE
It is difficult to specify the service life of a press brake tool because the material, plate thickness, and tool cannot be fixed. The tool maker does not specify the guaranteed life because it is affected by the handling of the tool (installation, centering, etc.).
Therefore, “regrinding” will be described as one of the maintenance methods to extend the life of the tool even a little.
〔 REGRINDING 〕
It is a basic standard for regrinding punches.
- 1.The amount of regrinding once is about 0.3mm to 0.5mm.
- 2.The number of tools that can be regrind is usually up to four times. Depending on the condition, it may be possible 5 times.
When tools are used side by side, it is necessary to regrind multiple pieces at a time, as a matter of principle,
in order to obtain “accuracy” after regrinding. In that case, regrinding is performed based on the tool that is most worn,
so it may be necessary to regrind about 0.5 mm or more at a time.
The relief of the cutting edge must be about 1 to 1.5 mm. This is because when considering spring-back,
it is necessary to bend deeply.
Punch tip wear
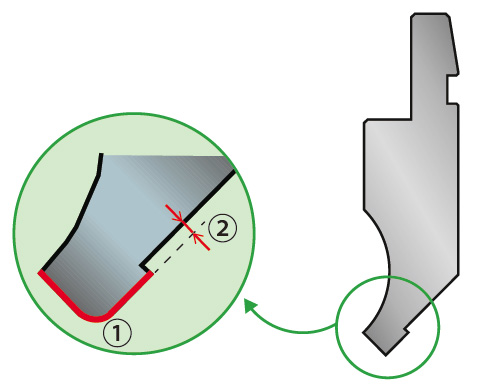
- 1.Tip wear
- 2.Grinding of relief part
Die shoulder R wear
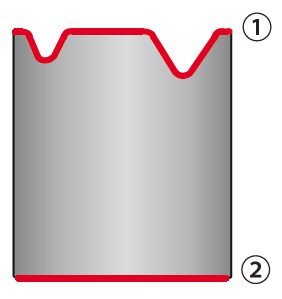
- 1.Grinding of shoulder R part
- 2.Grinding the bottom, depending on the situation
For tools, reducing the amount of grinding at one time and repeating the number of times will lead to longer life.
Consider the following as a method of extending the tool life other than re-grinding.
- 1.Use the tool with a margin for withstand pressure limit.
- 2.Does not form rust.
- 3.When storing the tools side by side, place them on a stable material without scratches such as timber under the tools.
- 4.Do not bend using only a part of the tool.
〔 About rust 〕
Rust is a phenomenon in which rust occurs on the surface of a metal due to the environment in which the metal is placed, and the appearance and functions are impaired.
As erosion progresses, the strength drops remarkably.
When press brake tool are rusted and eroded, that parts are liable to wear, and lose their balance to break easily.
If you find rust, we recommend that you remove it quickly and protect it with a rust inhibitor.
Tool with rust
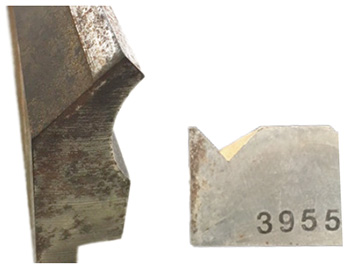
Causes of tool pressure reduction
- ◆When making improvements to the tool, such as “recessing” or “notching” ...
It is often found in tools that are close to the forming shape and perform bending. - ◆When heat is applied and hardness decreases ...
If continuous SUS processing is the main process, a “tempering phenomenon” due to frictional heat may occur. - ◆If there is a crack ...
Do not use it because it is often found in deformed tools and may cause damage.
Tool with deformed bending edge
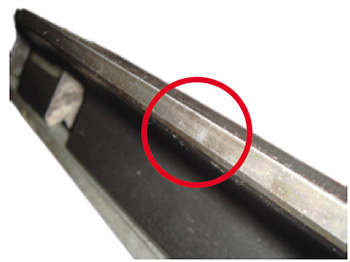
INFORMATION ON MEASURES PRODUCTS
Conic offers an original press brake tool “EURO” specializing in long life.
![]() |
The hardness of the punch and die bending edges has been increased to achieve an incredibly long life. |
---|---|
![]() |
A high-height type with a punch height of 120 mm, which has the same hardness as the EURO series tools. |

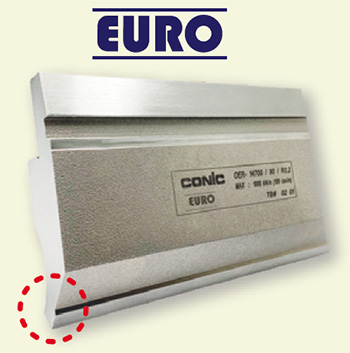
Feature
- 1.Approximately 4 times longer life than conventional tool (standard tool).
- 2.Due to high hardness, scratches are less likely to occur.
- 3.Significantly reduced the cost of re-grinding.
- 4.Reduced man-hours required for tool replacement.
Example: | Comparison data when bending by H Electric Company. (ER-00402 L=835 SUS t=1) |
---|
- ●Conventional tool (Standard tool): Approximately 200,000 times
(until the first re-grind) - ●EURO tool: It could be bent over 800,000 times without re-grind. As a result,
re-grinding cost can be reduced compared to standard dies.
The forming section has been made even harder with our proprietary technology.
Please feel free to contact us for the details of the introduced tools.
vol.1 TYPE OF PRESS BRAKE TOOLS
vol.2 ABOUT V - BENDING TYPE
vol.3 PREPARATION FOR BENDING 1
(TONNAGE CHART , MINIMUM FLANGE LENGTH, V width selection)vol.4 PREPARATION FOR BENDING 2
(Punch marking example, V - BENDING FORCE CALCULATION FORMULA)vol.5 THE FEATURES OF BENDING
(BENDING ALLOWANCE, SPRING - BACK)vol.6 ABOUT TOOL SELECTION
(STEPS FOR CHOOSING A TOOL, STUDYING FROM THE DRAWINGS, READ DETAILS FROM DRAWINGS)vol.7 ABOUT TOOL INSTALLATION
(TOOL INSTALLATION PROCEDURE, ALIGNMENT PROCEDURE)vol.8 PROBLEMS OF BENDING
(DIMENSIONAL DEFECT AND ANGLE DEFECT, GUIDELINS FOR RE-POLISHING, COUNTERMEASURES OTHER THAN REGRINDING)vol.9 PROBLEMS OF BENDING 2
(ANGLE DEFECT, MACHINE MAINTENANCE)vol.10 PROBLEMS OF BENDING 3
(COUNTERMEASURE FOR CRACK / FRACTURE)vol.11 PROBLEMS OF BENDING 4
(SPRING-BACK MEASURES, WORK WARPAGE MEASURES, SHEARING METHOD AND WARPAGE TENDENCY BY SHEET METAL MACHINE)vol.12 TYPES OF BENDING SHAPES
(HEMMING BENDING, STEP BENDING)vol.13 BENDING FAQ 1
(TOOL INTERFERENCE, MINIMUM FLANGE LENGTH)vol.14 BENDING FAQ 2
(ABOUT TOOL SELECTION)vol.15 ABOUT TOOL MANAGEMENT
(EXAMPLE OF TOOL MANAGEMENT, EXTENDING TOOL LIFE)vol.16 PROBLEMS OF BENDING
vol.17 PROBLEMS OF BENDING
(BENDING BUMP MEASURES)vol.18 PROBLEMS OF BENDING