vol.8 PROBLEMS OF BENDING
(DIMENSIONAL DEFECT AND ANGLE DEFECT, GUIDELINS FOR RE-POLISHING, COUNTERMEASURES OTHER THAN REGRINDING)
Even with advances in machines, there are still problems with bending.
This is because bending is largely dependent on the skill of the worker.
This time, let's consider a typical failure occurrence example.
DIMENSIONAL DEFECT AND ANGLE DEFECT
If the bending process (number of times) is large, defective dimensions and defective angles are likely to occur.
These lead to problems such as spring-back and sagging, which will be described later, and these causes are not only molds but also machines, processed materials, plate thickness, etc.
The countermeasures are different for each cause, so it cannot be said unconditionally, but this time we will explain the tool cause.
〔 DIMENSIONAL DEFECT 〕
Wear due to repeated use accounts for many of the causes.
In the tool, the punch tip radius and the die shoulder radius are worn.
As the wear proceeds, the bending allowance will change, which may lead to defective product dimensions.
In addition, it may be difficult to identify the cause when using a combination of tools with either one of the punch and die worn.
Defective example: SUS 1.5t, bending process in 8 steps resulted in a difference of ≒ 0.32mm
from the dimension in the developed view (within tolerance).
A single bending gives an error of 0.04mm.
And then, when the tool was inspected, it was found that the tip of the punch was worn at R0.2 → 0.6 and the die shoulder was at R0.6 → 1.0.
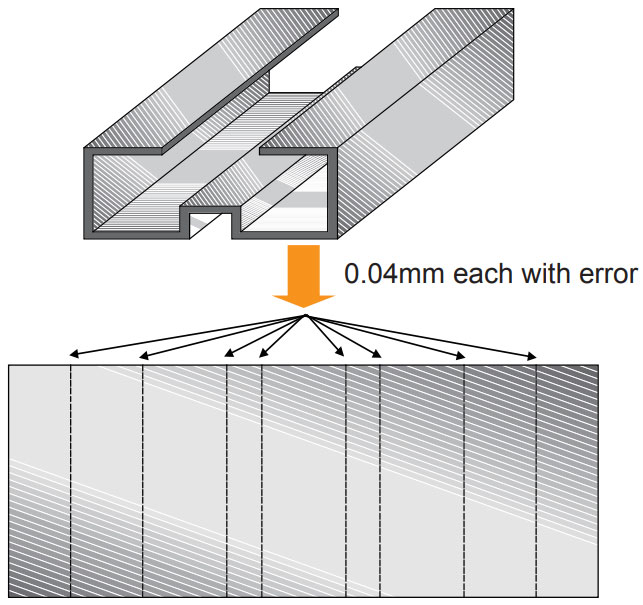
Wear progresses without the operator's knowledge.
It is difficult to judge which of the punches and dies needs to be reground by the appearance alone.
To accurately measure the accuracy of the worn tool (punch tip R, die shoulder R), specialized measuring instruments are required, which is difficult for users.
As a countermeasure, it is important to check the accuracy by trial bending and to perform regular regrinding.
The next page describes measures.
GUIDELINES FOR RE-POLISHING
If any of the following phenomena are observed, this is an indication that the tool is worn.
- 1.When the finished dimensions change during the same lot creation.
- 2.When “the deflection at the center” (*1) becomes noticeable.
- 3.After bending of SUS material.
- 4.A tool that is frequently used but has not been re-polished regularly.
- 5.Tool with rust.
(*1) What is “the deflection at the center”?
In bending, the bending angle at the center increases as shown in the figure.
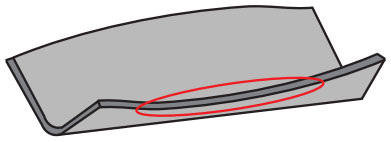
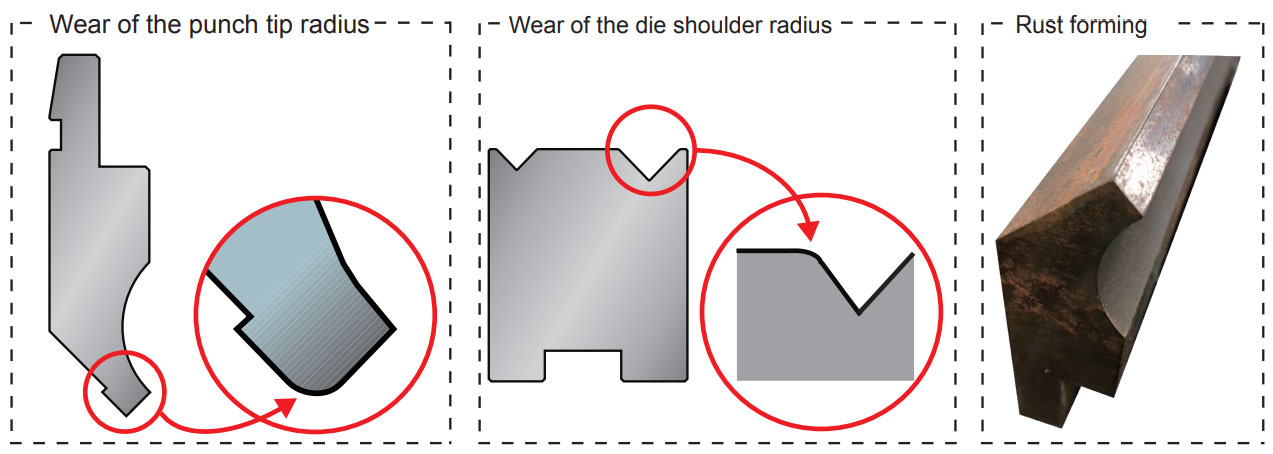
Wear of the punch tip radius
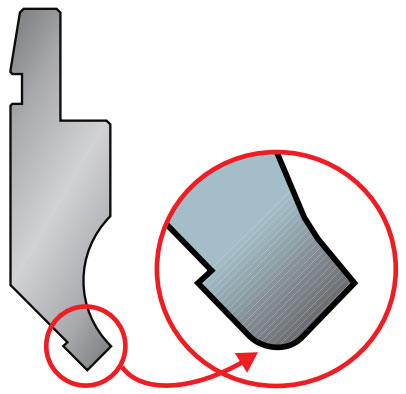
Wear of the die shoulder radius
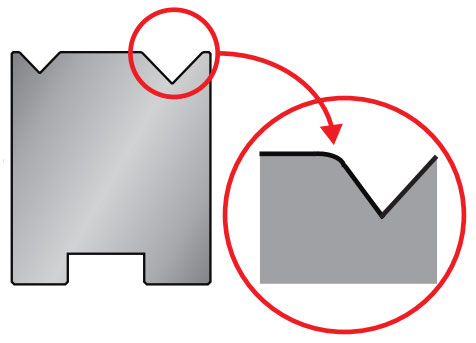
Rust forming
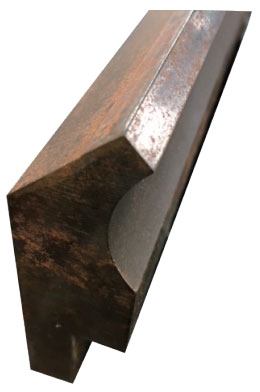
COUNTERMEASURES OTHER THAN REGRINDING
- 1.Perform the aligning operation again. If the center is misaligned, the wear proceeds. Finding early can return the dimensions.
- 2.If you are using sectionalized 2V die rails, double check that there are no gaps between the rails.
- 3.In the case of step bend, change the tool mounting position.
Machine cylinders are pressurized at both ends and pressurized at the center, but the bending accuracy may vary slightly at the position where the product is bent.
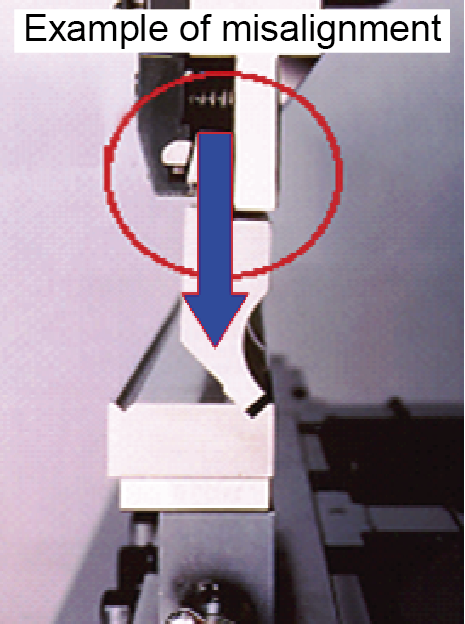
CHECKING THE MACHINE
Read the maintenance information in the machine's instruction manual, start the hydraulic pump,
replace working oil, retighten screws, and perform daily maintenance.
If you notice any abnormality in the machine, ask the machine manufacturer for inspection and repair.
vol.1 TYPE OF PRESS BRAKE TOOLS
vol.2 ABOUT V - BENDING TYPE
vol.3 PREPARATION FOR BENDING 1
(TONNAGE CHART , MINIMUM FLANGE LENGTH, V width selection)vol.4 PREPARATION FOR BENDING 2
(Punch marking example, V - BENDING FORCE CALCULATION FORMULA)vol.5 THE FEATURES OF BENDING
(BENDING ALLOWANCE, SPRING - BACK)vol.6 ABOUT TOOL SELECTION
(STEPS FOR CHOOSING A TOOL, STUDYING FROM THE DRAWINGS, READ DETAILS FROM DRAWINGS)vol.7 ABOUT TOOL INSTALLATION
(TOOL INSTALLATION PROCEDURE, ALIGNMENT PROCEDURE)vol.8 PROBLEMS OF BENDING
(DIMENSIONAL DEFECT AND ANGLE DEFECT, GUIDELINS FOR RE-POLISHING, COUNTERMEASURES OTHER THAN REGRINDING)vol.9 PROBLEMS OF BENDING 2
(ANGLE DEFECT, MACHINE MAINTENANCE)vol.10 PROBLEMS OF BENDING 3
(COUNTERMEASURE FOR CRACK / FRACTURE)vol.11 PROBLEMS OF BENDING 4
(SPRING-BACK MEASURES, WORK WARPAGE MEASURES, SHEARING METHOD AND WARPAGE TENDENCY BY SHEET METAL MACHINE)vol.12 TYPES OF BENDING SHAPES
(HEMMING BENDING, STEP BENDING)vol.13 BENDING FAQ 1
(TOOL INTERFERENCE, MINIMUM FLANGE LENGTH)vol.14 BENDING FAQ 2
(ABOUT TOOL SELECTION)vol.15 ABOUT TOOL MANAGEMENT
(EXAMPLE OF TOOL MANAGEMENT, EXTENDING TOOL LIFE)vol.16 PROBLEMS OF BENDING
vol.17 PROBLEMS OF BENDING
(BENDING BUMP MEASURES)vol.18 PROBLEMS OF BENDING