vol.11 PROBLEMS OF BENDING 4
(SPRING-BACK MEASURES, WORK WARPAGE MEASURES, SHEARING METHOD AND WARPAGE TENDENCY BY SHEET METAL MACHINE)
This time, let’s consider spring-back and warpage measures.
SPRING-BACK MEASURES
Spring-back is a phenomenon in which the bending angle rebounds when the pressure is removed after bending. Here are three typical examples of measures.
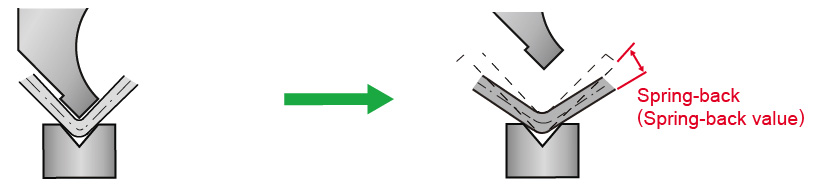
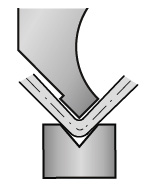

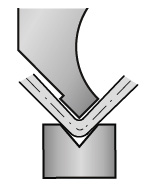
MEASURES 1
Two-stage bending in which two bends are made with one stroke.
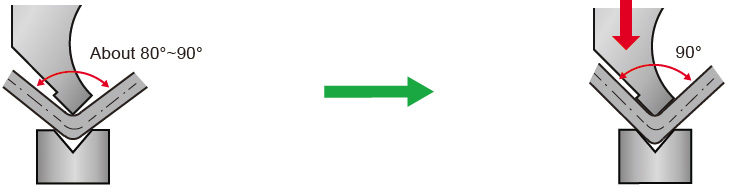
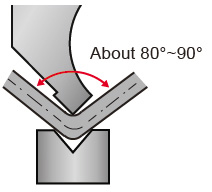

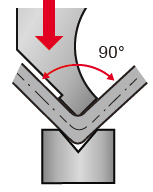
- 1.In the first stage, bend to about 80° to 90° as preliminary bending.
Once the pressure is released, spring-back occurs intentionally.
- 2.The specified angle can be obtained by applying pressure again without raising the punch.
MEASURES 2
Corner pressing method (striking)
It is also called a striking method, and protrusions called striking are provided at both corners of the cutting edge of the punch,
and spring-back is prevented by approaching the bending of the coining method.
*This type has a special punch shape, but is suitable for mass production.
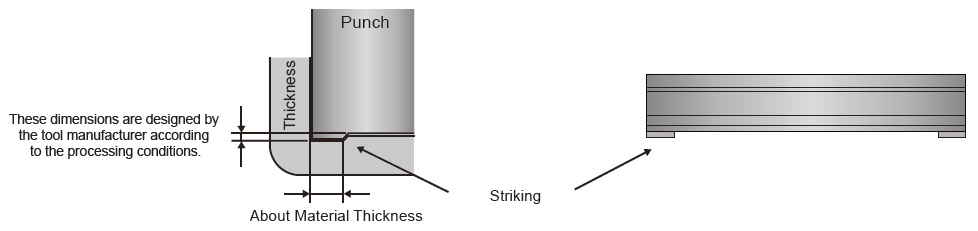
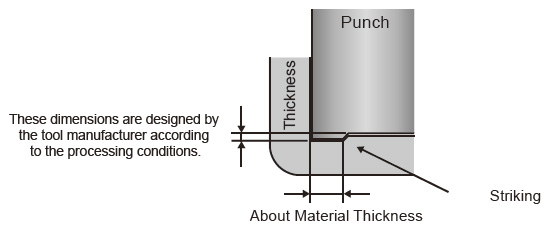
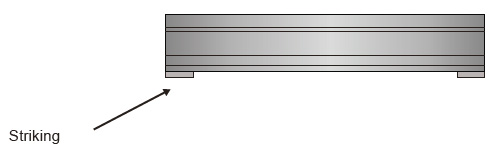
MEASURES 3
Provide V-notch (Edge preparation)
A method in which a V-notch (V-shaped recess) is pre-attached to the work material in the previous process, and pressed so that the edge of the punch hits that part.
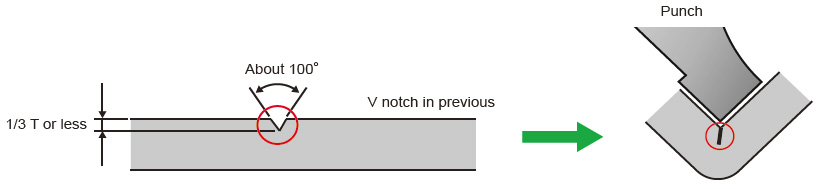
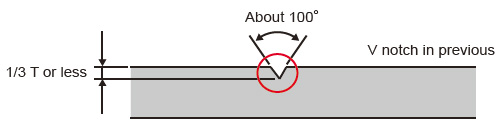

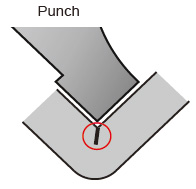
WORK WARPAGE MEASURES
- 1.The tool used is re-grinding at the same time.
*Since several tools are often used side by side, process with the accuracy between tools. - 2.Bend with coining.
- 3.If you are using an older machine, adjust the shim between the die and holder where warping occurs.
After bending once, bend again, so it is necessary to pay attention to tool positioning and shim thickness setting. - 4.If you are using an old machine, avoid bending at the position where the pressurized cylinder is, and perform bending.
- *For 3 and 4, measures are taken on the machine itself in the current machine, and adjustments can be made on the console or on the mechanism of the machine body.
Precautions when using old machines
- ■The longer material bending they are the more manual corrections is needed.
- ■As a guide, an error of 0.5mm for SPCC and 1.5 to 2.0mm for SUS is given for bending of 1m or more.
- ■However, it depends on the specifications of the mold and machine, and the material to be processed, so it is necessary to collect data with in a company.
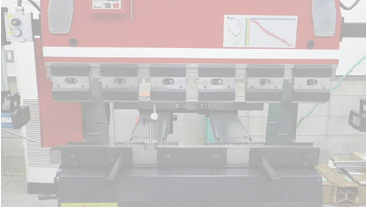
Old machine image
SHEARING METHOD AND WARPAGE TENDENCY BY SHEET METAL MACHINE
Cutting by Turret Punch Press ![]() |
Cutting by laser processing ![]() |
|
The direction of the warpage | Both ends upward | Both ends downward |
The degree of the warpage | Smaller than laser processing | Larger than Turret Punch Press & Punch Press machine |
Bending speed & warpage | If the bending speed is reduced, the warpage tends to decrease. | If the bending speed is increased, the warpage tends to decrease. |
Material & amount of warpage | SPCC < SUS | SPCC < SUS |
Cutting by Turret Punch Press ![]() |
|
The direction of the warpage | Both ends upward |
The degree of the warpage | Smaller than laser processing |
Bending speed & warpage | If the bending speed is reduced, the warpage tends to decrease. |
Material & amount of warpage | SPCC < SUS |
Cutting by laser processing ![]() |
|
The direction of the warpage | Both ends downward |
The degree of the warpage | Larger than Turret Punch Press & Punch Press machine |
Bending speed & warpage | If the bending speed is increased, the warpage tends to decrease. |
Material & amount of warpage | SPCC < SUS |
* The amount of warpage differs depending on the thickness and material.
CONCLUSION
Problems in bending are often caused by “spring-back” and “defective angle”, including “crack” of Vol. PB-10, and cannot be solved only by calculation and tool accuracy.
In fact, the reality is that more is being dealt with by “experience”.
Advances in machinery and analysis software are evolving, but in fact, correction after trial is indispensable.
It is necessary to respond based on various experience know-how depending on the situation.
vol.1 TYPE OF PRESS BRAKE TOOLS
vol.2 ABOUT V - BENDING TYPE
vol.3 PREPARATION FOR BENDING 1
(TONNAGE CHART , MINIMUM FLANGE LENGTH, V width selection)vol.4 PREPARATION FOR BENDING 2
(Punch marking example, V - BENDING FORCE CALCULATION FORMULA)vol.5 THE FEATURES OF BENDING
(BENDING ALLOWANCE, SPRING - BACK)vol.6 ABOUT TOOL SELECTION
(STEPS FOR CHOOSING A TOOL, STUDYING FROM THE DRAWINGS, READ DETAILS FROM DRAWINGS)vol.7 ABOUT TOOL INSTALLATION
(TOOL INSTALLATION PROCEDURE, ALIGNMENT PROCEDURE)vol.8 PROBLEMS OF BENDING
(DIMENSIONAL DEFECT AND ANGLE DEFECT, GUIDELINS FOR RE-POLISHING, COUNTERMEASURES OTHER THAN REGRINDING)vol.9 PROBLEMS OF BENDING 2
(ANGLE DEFECT, MACHINE MAINTENANCE)vol.10 PROBLEMS OF BENDING 3
(COUNTERMEASURE FOR CRACK / FRACTURE)vol.11 PROBLEMS OF BENDING 4
(SPRING-BACK MEASURES, WORK WARPAGE MEASURES, SHEARING METHOD AND WARPAGE TENDENCY BY SHEET METAL MACHINE)vol.12 TYPES OF BENDING SHAPES
(HEMMING BENDING, STEP BENDING)vol.13 BENDING FAQ 1
(TOOL INTERFERENCE, MINIMUM FLANGE LENGTH)vol.14 BENDING FAQ 2
(ABOUT TOOL SELECTION)vol.15 ABOUT TOOL MANAGEMENT
(EXAMPLE OF TOOL MANAGEMENT, EXTENDING TOOL LIFE)vol.16 PROBLEMS OF BENDING
vol.17 PROBLEMS OF BENDING
(BENDING BUMP MEASURES)vol.18 PROBLEMS OF BENDING